Background and Motivation
The Grouted Shear Stud Connection
In steel bridge substructures, the conventional practice for connecting the steel columns/piles to the cap beam was through a direct weld. This is shown in the figure below. The yellow oval encircles the region where the column is directly welded to the cap beam.
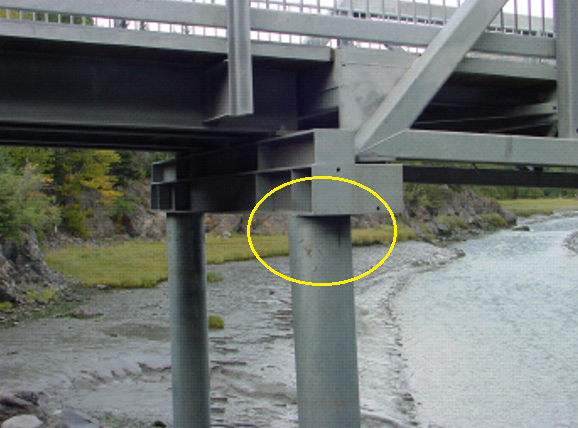
Figure 1: From a bridge in Alaska, USA
However, these kind of connections were tested in the lab a few years ago under cyclic lateral loading, i.e., loading cycles along the longitudinal axis of the cap beam. These tests resulted in what you see here:
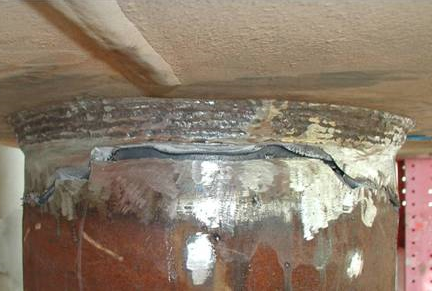
Figure 2: From a laboratory test
The columns ruptured at or near the weld region. This is what we call as a brittle mode of failure which is undesirable in any structure. To add to that, these columns were not even able to develop their full section ductility when they failed. In other words, this type of failure limit state can be regarded as “premature”. Hence a conclusion was that the directly welded connections cannot be used in seismic design applications.
After going through a few alternatives, the researchers converged onto the grouted shear stud (GSS) connection which was able to successfully move the failure away from the welded region thereby inducing plastic hinging at the column section with maximum moment. This is a desirable failure mode since it is ductile.
The GSS connection looks like a socket type connection as shown here:
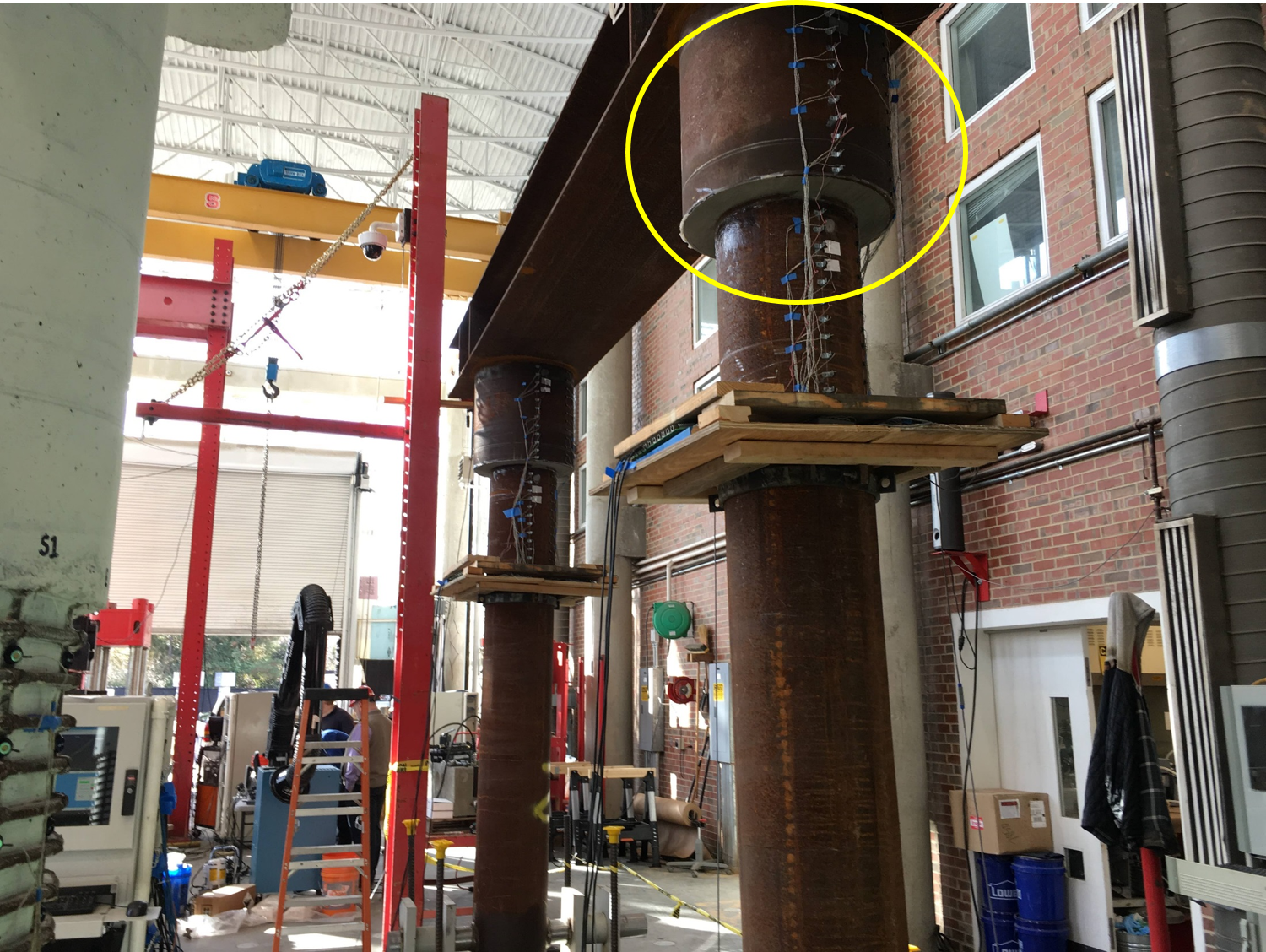
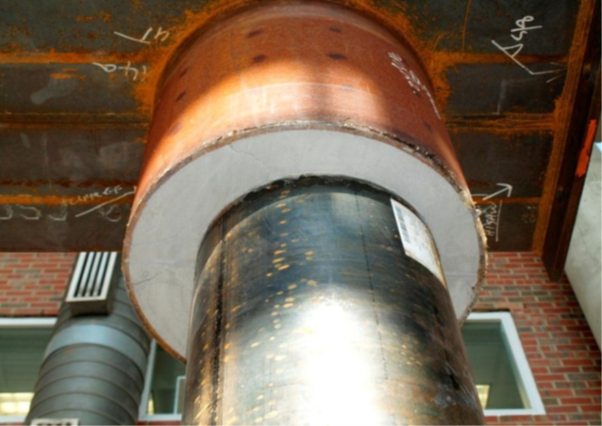
Figure 3: The GSS connection on an experimental specimen
A larger diameter pipe stub is shop welded onto the cap beam first.
Note: A large part of field welding is eliminated if one uses this connection which is desirable from cost and quality control standpoint.
After this, the cap beam + stub assembly is brought to the site where the pile columns will already have been erected. The cap beam + stub assembly is then lowered onto the columns such that the column tops fit into the socket created by the larger diameter stub. The annular region that is hence formed is then grouted with a high strength cementitious grout. The larger diameter connection section acts as a composite section resisting a much larger moment than the capacity of the pile section.
To facilitate this composite action, shear stud connectors are welded on the inside of the stub as well as the outside of the pile top as shown:
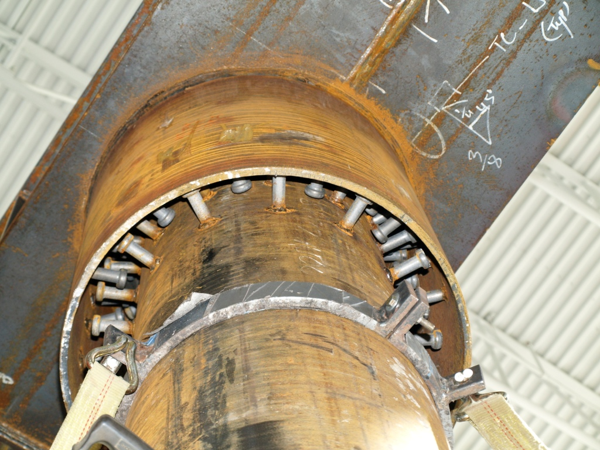
Figure 4: Notice the shear studs welded within the connection
By now, I presume, you have formed an idea of what the GSS connection looks like. So how did it fare? Here is the picture of a specimen that failed in a ductile mode:
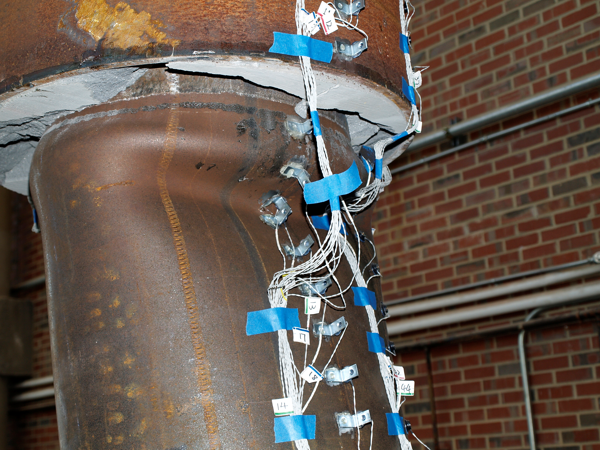
Figure 5: Failure via plastic hinge formation = Good!
There is some spalling of the grout material but the connection remained fairly undamaged. All the damage was concentrated just below the connection: plastic hinge formation followed by local pile wall buckling. Here is a sample force-displacement hysteresis curve of two tests on similar specimens:
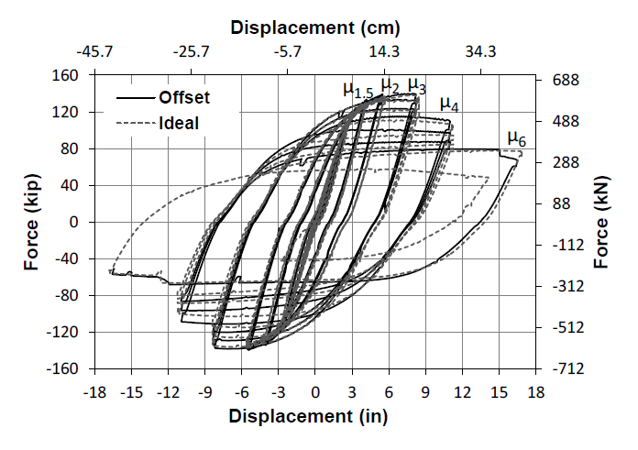
Figure 6: Gradual drop in strength and failure at high ductility = Promising!
The specimens seemed to take lateral loading pretty well. Hence, the conclusion was that the GSS connection can potentially be a good candidate for seismic design.
Ok, so that was a summary of the GSS connection: what it is, how it came into being and how well it assisted in lateral load resistance.
So why not start widespread use?
Despite its shining performance under cyclic lateral loading, the GSS connection has not been fully understood to be employed in actual practice.
The grout variable
High strength cementitious grouts are conventionally used as filler materials in small size applications such as reparing damaged concrete, sockets for dowell rebars, bridge keyway joints etc. One major application of this material is to level floor surfaces to install large machines on machine foundations. However, there are no studies in literature that have investigated large scale applications of cementitious grouts such as that in a GSS connection. To add to that, there are also no studies that have looked at the service life of cementitious grouts in large scale applications. In an application such as the GSS connection, the service life of the grout could be potentially critical since it provides the only load path between the column and the cap beam. Hence, more experiments are warranted before high strength grouts could be used in the GSS connection.
Consequences of deteriorated grout
When talking about the service life of the grout, one has to also ask the question how well it maps on to the service life, or structural performance of the entire lateral load resisting system. This is important because it may be the case that a damaged GSS connection could still perform its function retaining the structural integrity of the global system. This has also not been investigated yet.
So what can we do about it? How can we ensure that the GSS connection is indeed the right candidate for the job?
Research Approach
Ideally…
The ideal approach would be to first test some structure that employs the GSS connection in laboratory conditions. Subsequent specimens should then be exposed to extreme weather conditions for a long time, say 20, 50 to 100 years and then test them for their structural performance. Needless to say, this is impractical.
A more practical approach
Here is what we did. The first step remained the same, i.e., test a structural specimen with GSS connections under laboratory conditions. Then for the second specimen, we physically simulated a deteriorated state of grout within the GSS connection. The assumption is that this simulated deterioration is representative of the deterioration casued by years of extreme weather exposure.
How did we simulate deterioration?
Engineers have been using lightweight concrete for a few decades now. Among the many ways that you can make concrete lightweight, one is to add to it lightweight aggregates. One such aggregate is called expanded polystyrene (EPS). These are small beads with extremely low density like styrofoam as shown here:
Figure 7: EPS beads
When a part of normal weight concrete is replaced by these material, the total weight reduces. Researchers have also studied its impact on other properties of concrete as well. What they found was that adding EPS to a concrete mix not only reduces its weight, but also its compressive strength and elastic modulus. This property of EPS is interesting for us because of the following. Cold climate exposure of grout leads to grout deterioration through freeze and thaw cycles. The consequence is a reduction in the grout compressive strength and elastic modulus. So the idea then became, why not use EPS to induce in our grout, a large reduction in both elastic modulus and compressive strength, thereby simulating multiple years of service life.
Now you may ask, well don’t freeze and thaw cycles cause deterioration of grout in a completely different manner compared to adding EPS beads? This is true at a micro scale. Cracking in the grout due to freeze and thaw damage look nothing like a bunch of EPS beads being present in it. However, we are more interested at a macro scale. The question that we are trying to answer is that at the structural level, does the reduction in compressive strength and elastic modulus, or in other words deterioration, of the grout in the GSS connection cause a worse structural performance under lateral loading. Hence we proceeded with this approach.